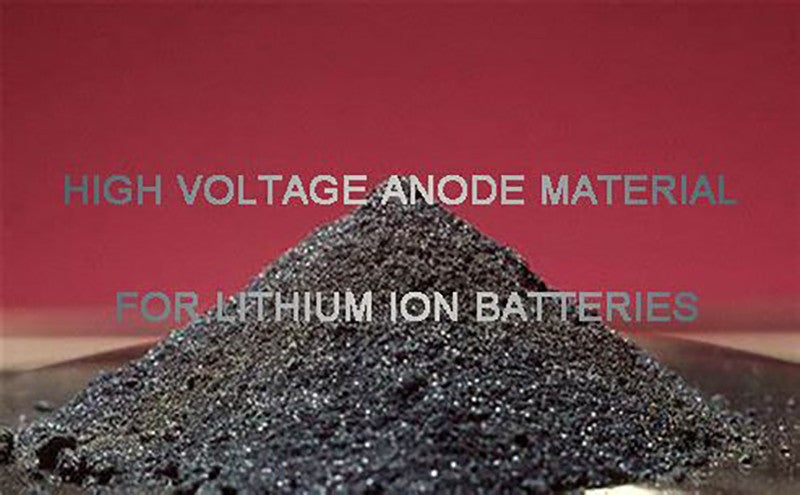
Main content:
Recently, Professors Yunhui Huang, Henghui Xu and Lixia Yuan of Huazhong University of Science and Technology published a review paper on Advanced Materials. The development of high energy density lithium-ion batteries (LIB) to meet the needs of the growing electric vehicle market has long been a global priority. One of the most effective strategies for improving the energy density of lithium-ion batteries is to increase the output voltage, which largely depends on the cathode material. As the most promising high voltage cathode materials for lithium ion battery (> 4 V vs Li/Li +), layered rich lithium oxide, rich nickel layer oxides and spinel oxides and high-voltage polyanionic compounds the positive faces severe test in four categories with high capacity and ability of rapid rate and long service life and improve the challenges faced by the output voltage.
This rarticle focuses on the key links of high voltage cathode materials from laboratory to industrial development. Firstly, the failure mechanism of the four materials is clarified, and the optimization strategy is emphasized, especially the solution that is easy to scale production. Then, in order to bridge the gap between laboratory and industry, cost management, safety assessment, actual battery performance assessment and sustainability of battery technology are discussed. Finally, the serious challenges and promising strategies for the commercialization of high voltage cathode materials are summarized to promote the large-scale application of lithium ion battery high energy density .
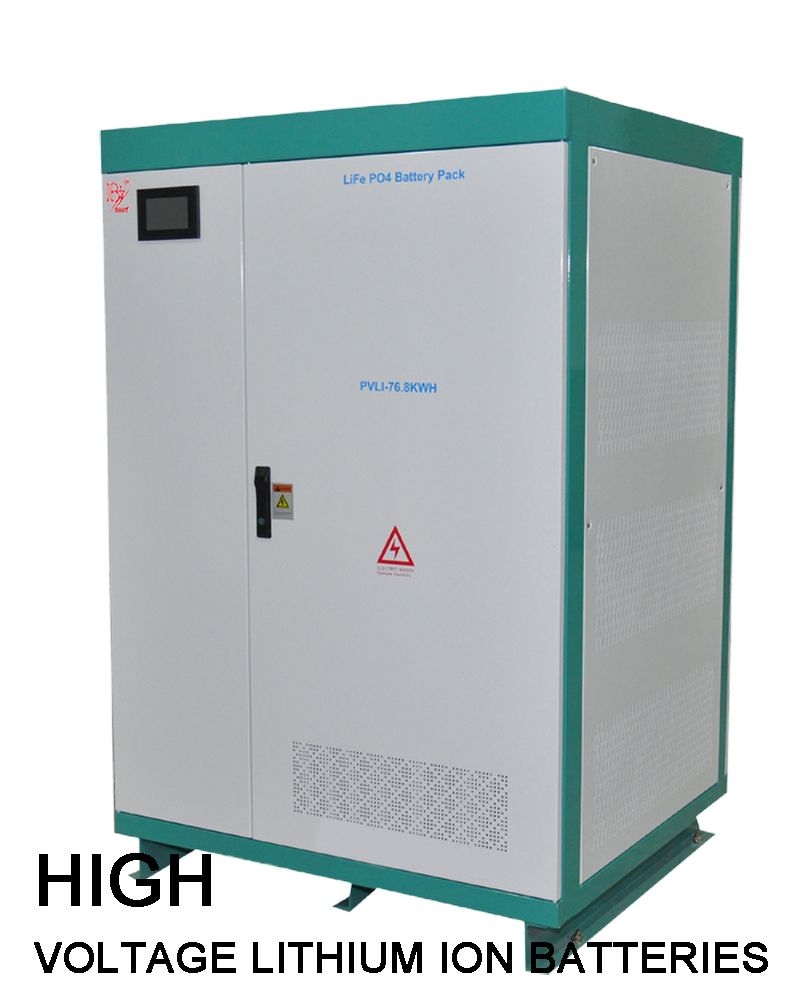
Accelerating the shift from fossil fuels to renewable energy sources is now even more urgent in order to cope with growing energy shortages and environmental degradation. High energy density lithium ion battery plays an indispensable role in the construction of new energy structure. It is generally accepted that the energy density of lithium-ion batteries needs to be around 300 Wh/kg, or even 350 Wh/kg in a single cell level, to meet the needs of electric vehicles, smart grids and other fields.
Now The nickel-rich layered oxide (charging voltage < 4.5V) has been successfully commercialized and gradually applied to electric vehicles. If the charging voltage can be raised to 4.5V or higher, the energy density will be further improved. When paired with a graphite-silicon anode, the energy density of high-voltage lithium-ion batteries can reach 350 Wh/kg at the battery level, and can be further increased to 500 Wh/kg if lithium metal is used instead of the anode.
However, when we talk about stability high voltage cathode materials is not as good as that of traditional cathode materials (LiCoO2, LiFePO4). Therefore, it is necessary to study high voltage cathode materials failure mechanism in depth, and corresponding effective optimization strategies are needed. At the same time, the battery safety assessment and advanced recycling technology of waste batteries also urgently need to realize the sustainable development of LIBs. As mentioned above, the commercialization for high voltage cathode materials still faces the following challenges:
1.Failure mechanism analysis
The cycling stability of the high voltage cathode materials are not as good as that of the traditional cathode material, which is mainly due to the degradation happened in high voltage cathode materials and the decomposition of the electrolyte at the cathode/electrolyte interface. CEI is difficult to monitor due to its complex and dynamic structure. Cryo-electron microscopy, which has been developed in recent years, shows great ability in accurately characterizing the composition, thickness and element distribution of CEI, which provides a possibility for studying the structural evolution of CEI. While riding a bike. In addition, in situ characterization techniques such as in situ atomic force microscopy (AFM), in situliquid secondary ion mass spectrometry (IN-situliquid-SIMS), and in situ X-ray photoelectron spectroscopy (XPS) provide insight into the interface evolution between the positive electrode and electrolyte. In addition, electrochemical characterization techniques also play an important role in identifying failure mechanisms. For example, in situ quantitative studies of interface chemistry can be performed using a combination of atomic force microscopy, electrochemical quartz crystal microbalance (EQCM), and differential electrochemical mass spectrometry (DEMS) characterization.
2.Overall evaluation of electrochemical performance
It has been reported that high voltage cathode materials electrochemical properties can be significantly improved by surface coating, element doping and electrolyte optimization. However, test parameters, such as electrolyte volume and area-capacity load variations, were not consistent with industry requirements. In general, the area capacity reported at 5 C rate is less than 1 mAh cm-2 and the current density is less than 5 mA cm-2, much lower than the actual LIB (~ 4 mAh cm-2 and 20 mA cm-2). In addition, the amount of electrolyte should be controlled below 3 g AH-1 to achieve a high energy density of 350 Wh/kg. In addition, it is worth noting that the operating conditions of LIBs are complex and changeable in practical application. The operating voltage and current of the lithium-ion battery pack in an electric vehicle vary with the acceleration, deceleration, braking and idling of the vehicle. At this point, the lithium-ion battery pack must be able to withstand high current shocks and a quick switch from charge to discharge. Therefore, it is very important to test the dynamic performance of high voltage batteries.
3.Optimize battery safety standards
For use in electric vehicles, high voltage LIB faces safety issues, which is one of the biggest. The stability of cathode materials and electrolyte under high voltage needs to be greatly improved. In addition, the thermal runaway mechanism of high voltage battery under mechanical abuse, electrical abuse and thermal abuse needs further study. At the same time, relevant battery safety test standards should be established, such as extrusion test, overcharge test, short circuit test, puncture test, etc. In addition to operational safety, more attention should be paid to the safety of battery manufacturing. For example, when selecting electrolyte additives to improve the resistance of electrolyte to high voltage oxidation, low toxic or even non-toxic materials should be selected to reduce the harm to human health and the environment. In general, it is important to conduct rigorous safety assessments throughout the battery life cycle, from raw material production to battery use.
4.Construct the closed-loop recycling of LIBs
Due to the scarcity of cobalt, lithium, nickel and other metal resources, how to realize the second life application of batteries and efficient recycling of waste batteries is the key to realize the sustainable development of battery industry. In addition to the sustainable development of the battery industry, the efficient recycling of high voltage LIB is also beneficial to the reduction of battery cost. In future research, academia should strengthen cooperation with industry to optimize the recovery technology of spent lithium ion batteries and improve the battery recovery rate. Mature commercialization is still a long way off. The large-scale application of high voltage lithium ion battery, from the production of high voltage cathode material, to the manufacture of high voltage lithium ion battery, and then to the various application scenarios of high voltage lithium ion battery, all need the close cooperation of academia and industry. Secondary application and recycling of high voltage lithium ion batteries. Only in this way can high performance, low cost, high safety and sustainable development of high voltage cathode materials be commercialized on a large scale. Despite the challenges, the authors believe that with continuous efforts, it is only a matter of time before practical high voltage cathode materials become available one for use in high-energy battery systems.